Progressive failure prediction of woven fabric composites using a multi-scale approach
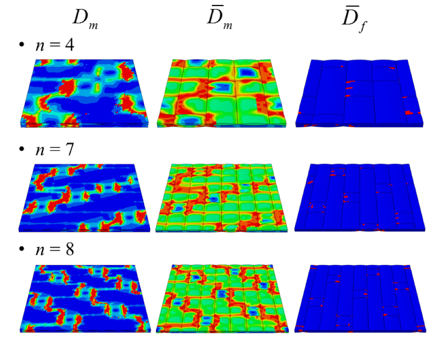
Keywords:
- Woven textile composites
- Weave pattern
- Micromechanics
- Progressive damage
Abstract
Finite element representative unit cell models are established for the study of progressive failure of woven fabrics: plain weave, twill weave, and satin weave. A multi-scale approach ranging from the meso-scale to micro-scale regime is used, providing the failure observation inside the constituents. The constituent stresses of the fiber and matrix in the warp and fill tows of the woven fabric unit cell are calculated using micromechanics. Correlations between meso-scale tow stresses and micro-scale constituent stresses are established by using stress amplification factors. After calculating micro-scale stresses, the micromechanics of failure damage model is employed to determine the progressive damage statuses in each constituent of woven fabric composites. For the matrix of tows, a volume-averaging homogenization method is utilized to eliminate damage localization by smearing local damages over the whole matrix region of the unit cell. Subsequently, the ultimate strength is predicted for woven composites with different tow architectures. The prediction results are compared with the experimental values, and good agreement is observed.